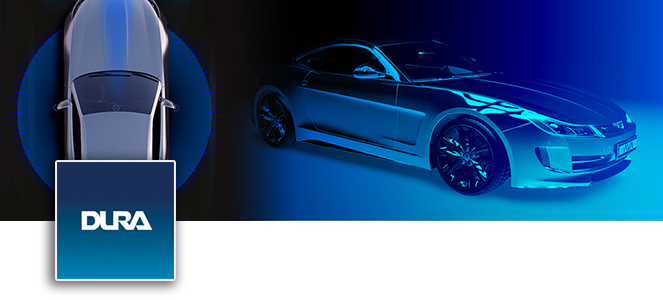
Launch Manager
- Responsible for assessing and tracking launch activities of new production lines
- Responsible representative of the plant for the transfer and the Cross Functional Team Coordinates and follows the tasks of the plant for ramp-up/changes
- Supports the status of the ramp-up or changes to the plant’s organisation and to the transfer or Cross Functional Team
- Reports the status of the ramp-up or changes to the plant’s organisation and to the transfer or Cross Functional Team
- Plans and co-ordinates the engineering, purchasing, financial controlling, manufacturing, process engineering, quality, maintenance and material function at the plant and external resources associated with project launches from Gate 2 to Gate 5 of APQP. Provides an on-site resource to overall Cross Functional Team Program Leader
- Protecting the production plant to ensure a smooth launch into production with the least financial risk through, monitoring of Scrap/Productivity/PPM
- Ensures the project timelines are achieved during a product transfers and new launches.
- Continuously analyses project resources and tasks to ensure compliance to Dura internal requirements and Customer Milestones.
- Escalates, in timely manner, unresolvable roadblocks to Program/Launch Manger and Plant Manager, for further assistance to ensure the project can be brought back on course.
- Communication with the production floor of newly launching lines, staffing needs for hire, volume needs in relation to timing.
- Ensure production floor is ready for new equipment arrival, working with Facilities, Floor Space Requirement Planning
- Identify, recommend, and implement changes to procedures to reduce cost and scrap.
- Audit systems for known systemic failures, Directs compliance with established precepts outlined within such standards as IATF 16949, ISO 14001 etc. 28.07.2014 Page 2 of 2
- Ensure project performance complies with budgeted performance as approved in the latest CPQA.
- Participates in Project budgeting, capital and strategic planning by providing information on project related requirements and capabilities.
- Review purchase requisitions to facilitate the project.
- Coordinates and communicates with plant scheduling function to ensure thorough understanding of capacity utilization and equipment/tooling shortcomings in order to meet customer demands.
- Coordinates the development and implementation of a proactive continuous improvement program, which effectively utilizes the Kaizen process and philosophy to optimize quality, productivity and profitability.
- Maintains overall responsibility for ensuring a safe, clean work environment and notifies appropriate support departments of actions required to improve the safety and material condition of the facility.
- Ensures the Plant Operation’s APQP deliverables are achieved as per the program time line and corporate APQP procedure.
- Completes and performs other duties/tasks as may be assigned.
- Education: Engineer specialized in mechanical engineering, electrical engineering, or similar
- Experience: Minimum 3 years of related experience.
- Understanding of production floor requirements and needs
- Verbal communication skills, including group presentation, negotiation, and influencing.
- Management skills, including planning and organization, decision making, problem solving, project management, delegation, and employee development.
- Knowledge of manufacturing methods and process improvement programs.
- Ability to establish and maintain effective working relationships with senior management, supervisors, and employees.
- Ability to prepare complex written reports and other documents
If you are interested, please send your CV using the Fast Apply option.
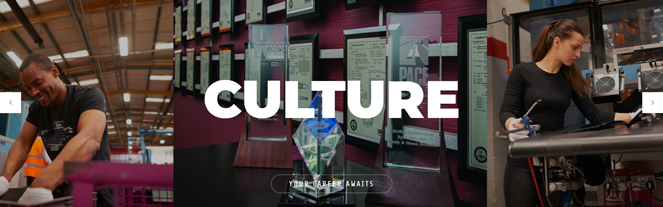
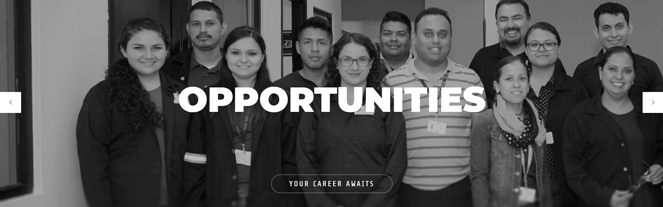
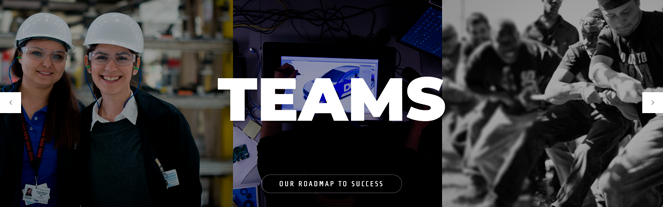